Foundry Equipment
Foundry Equipment is usually built to last forever, but sometimes new technology makes such gains in productivity, safety, ease of maintenance, or energy efficiency that an upgrade is warranted even if the old mule is still pulling. At New England Foundry Technologies, we strive to work with principles whose equipment will stand the test of time, and provide an upgrade path to keep your business competitive.
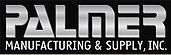
www.palmermfg.com
Palmer Brochure
Palmer Interactive Presentation
- No Bake Foundry Equipment
- Bulk Material Handling & Processing
- Foundry Engineering Services
- Parts
- Service
- 3D Printing Technology Center
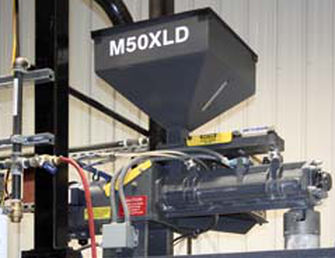
Palmer Manufacturing & Supply, Inc. is one of the world's most recognized producers of heavy-duty, high-quality, long lasting foundry equipment. PMS specializes in the production of No-Bake foundry equipment including sand mixers, molding systems, core room equipment, sand reclamation, mold handlers, complete foundry systems and engineering services. Palmer is aggressively designing equipment to enable higher throughput with more automation, less labor, and better ergonomics.
For questions about any of Palmer’s Divisions, contact us.
- Palmer Manufacturing & Supply, Inc.
No-bake foundry machinery, engineering and complete foundry systems. - Palmer Engineered Products, Inc.
Foundry consumables and tooling. - Palmer / Klein Technology Group
Pneumatic conveyors & mixers for foundry and rail sand. - Palmer Machinery
Industrial machinery and supplies. - Gorilla Machinery
Used industrial machinery, rebuilding, sourcing and inspection of equipment for foundry and general manufacturing. - Palmer Golf Systems
Sand mixers, dryers and processing equipment.
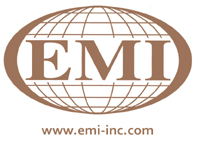
www.emi-inc.com
- Green Sand Molding
- Hot Box, Cold Box, Warm Box
- Core Makers
- Engineering
- Robotic Automation
- Parts
- Service
- Repairs
- Controls & HMI Updates
- Remanufacturing
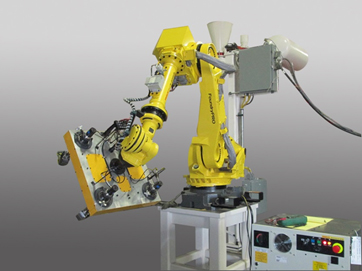
EMI has acquired well-known industry brands including Osborn, SPO, CE Cast, IMPACT, Sutter, Herman, and Harrison. The acquisition of these industry leading companies has resulted in unmatched industry knowledge and experience. They have pioneered innovative and patented improvements to these traditional equipment lines that bring longer life, lower maintenance, and higher productivity. EMI maintains a revolving inventory of common replacement parts to exact original OEM specifications and can typically respond with same day shipping for all our acquired brands.
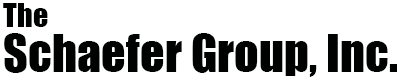
www.theschaefergroup.com
Schaefer Furnaces, FWS Refractories, Delta Control Systems
- Non-Ferrous Melting and Holding Furnaces
- Crucible Furnaces
- Dry Hearth Furnaces
- Low Pressure Casting Furnaces
- Transfer Ladles
- Molten Metal Transfer Launders
- Molten Metal Pumps and Valves
- Ingot Casting Lines
- Refractory Relines
- Refractory Components
- Service & Parts
- SCADA Control Systems
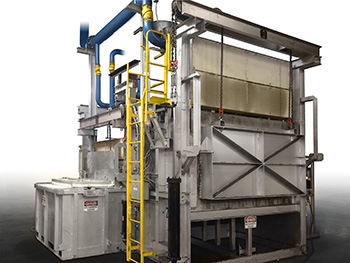
Schaefer Furnaces Division’s Custom Solutions and stock model furnaces from a holding a few hundred pounds to melting thousands of pounds per hour. Gas, Electric, or Propane. Ultra high energy efficiency systems. Designed for ease of clean-out and service. Integrated Degassing, Filtration. Suitable for sand, investment, and die casting.
FWS, Inc. – Refractory Services Division
FWS Inc Refractory Services Division has been providing refractory reline, parts, and services to all refractory industries since 1930.
Delta Control System Integration
Delta Control is an experienced systems designer of integrated control systems for industrial furnaces, chemical plants, wastewater treatment plants and any industry that requires a highly engineered system to control operations accurately, reliably and consistently. We design systems from single pumps to elaborate SCADA with PLCs & HMIs.
Interactive Virtual Reality Furnace Models
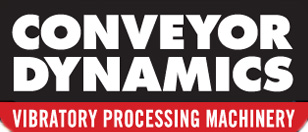
www.conveyordynamicscorp.com
Dynamically Balanced Vibratory Conveyors for: Transfer, Sorting, Mold Dump, Cooling, Accumulation, Slag Quench, Classification
- Shakeout Decks
- Furnace Charging
- Shot Blast Discharge
Conveyor Dynamics is a leading manufacturer of vibratory conveyors and processing equipment. Whether you’re charging, feeding, transferring, screening, sorting, cooling or quenching, Conveyor Dynamics can develop a solution that will improve production and your bottom line.
At the heart of each machine lies Conveyor Dynamics’ proprietary Dyna Sync Dynamic Drive System™. This advanced technology allows us to build equipment that is quieter, more dependable, and more adaptable than traditional vibratory equipment. See the Nickle Test video!
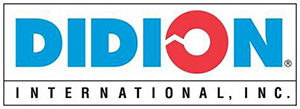
http://www.didion.com/
- Rotary Processing Equipment for the Foundry Industy: Media Polishing Drums
- Sand / Casting Separators / Lump Crushers
- Sand Screens
- Blending
- Cooling
- Dryers
- Carbon Separators
- Thimble Cleaners
- Coating Application Drums
- Dross / Slag Reclaimers
Didion - Leaders in Rotary Processing Equipment since 1974. Rotary systems are quieter, easy to install, have cheaper maintenance and utilities, and offer superior performance for many applications in the foundry industry.
Extremely fast returns on investment with systems that can reclaim 97% of sand
Case Study
Slag Reclamation systems with payoff periods of a couple months
Case Study
Klein Plug Flo ® pneumatic conveyors, batch mixing, and cooling/classification for the foundry and rail sand industry. Plug flow conveyors have lower energy demand, lower transport velocitys, less materials degradation and pipe wear – allowing for the use of lower air pressure, standard schedule 40 pipek and still claim lower maintenance on systems up to 20 tons per hour. Sand and other material can be conveyed to multiple destinations via PLC controls.
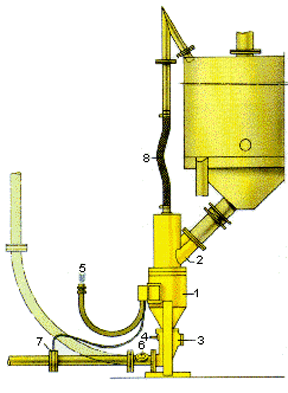
Please see kleinpalmer.com for more information.
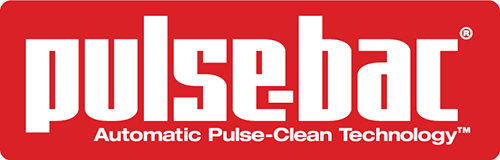
Pulse-Bac
Pulse-Bac solved the loss of suction that occurrs with most vacuums used in industry, caused by the filter becoming clogged with fine dust and debris and cutting off the airflow to the vacuum motor. Pulse-Bac vacuums are readily available innovative, high-quality products. The company is dedicated to helping professionals in many different industries find the best dust collection solutions to increase productivity and protect their health. Watch this Silica compliance Video to see the Pulse-bac system in action. Various sizes available for floor sweeping, dust collection from tools, and portable job site cleanup.
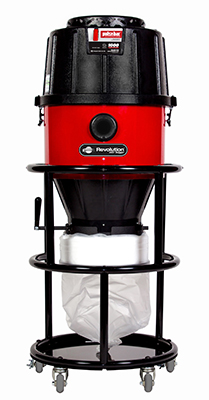
Please see kleinpalmer.com for more information.