In the world of tech companies, there are great products, and great people. Every once in awhile, you find companies where great products are made by great people – and that is probably the top reason that we are so happy to make this announcement.
The “vision” behind the line card for New England Foundry Technologies is to supply a toolkit for foundries who plan to be around for generations to come. Some of those tools are the same ones that have been around for decades or even centuries (sands, patterns, etc.). But many of the tools that will be used are essentially newer, faster, safer, and a more cost effective means of getting the job done. 3D printing is one of those “new” tool kits, and it has a lot of versatility to bring to the foundry market.
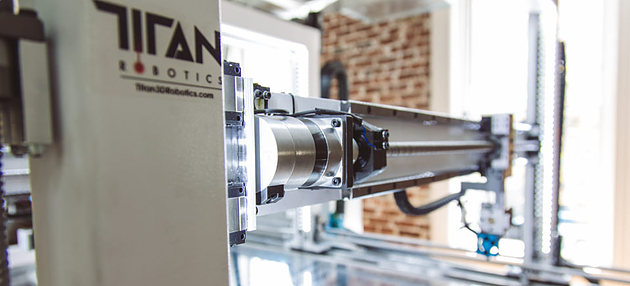
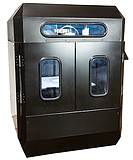
Titan 3D Robotics makes large format plastic 3D printers that are fast, high quality, and still surprisingly affordable. Their printers run on a wide range of plastic filaments. Their partnership with Push Plastic assures the top performance with Titan systems. Titan’s flagship line, the Atlas, comes in standard build sizes ranging up to 42”x42”x48”. The Hyperion, while slightly smaller, offers higher resolution and a lower price tag. The surface finish of the parts is quite good, as it the accuracy.
Titan also provides an option not available from most 3D Printer companies; they will make a build area to suit your target envelope. (As I write this, I’m expecting a request for a 60”x96”x48” printer to show up.) You can see more about their product lines at www.titan3drobotics.com
The New England Foundry Technologies line card already contains 3D sand printing – so you may wonder, “why carry both?” That’s something that we definitely thought about, and the answer makes complete sense when you stop to think about it – these are two highly complementary technologies, each with their own current strengths, and each with their own potential for future application development
With plastic printers, you can quickly and affordably make patterns & tooling. You can also make fit & function prototypes, which can be handy for communication in house or with your customers. You can get some work off of your pattern maker’s plate, by printing sections for gates, risers, filters, etc. Coreboxes can be printed. And, believe it or not, some printed plastic patterns can run for a while in a continuous molding line with either green sand, cold box, or no-bake systems. You can use plastic printers to generate custom shapes for risers, chills, etc. with a flexibility that you won’t get from a CNC. These parts can all be used with your CURRENT tooling – so plastic 3D printing is a good gateway into additive manufacturing for foundries that might not be ready to make the investment into 3D sand printing yet. If you like to tip-toe in, they are the perfect way to get your feet wet.
Plastic printers, in combination with 3D sand printing, also offer a hybrid approach for medium volume, or larger size parts than would fit in the sand printer. Patterns for copes & drags can be printed in parallel with the sand cores – giving an optimized approach to mold making, with the most cost effective solution being provided by each technology. Titan3D offers a bright future for plastic printing. An exciting new pellet extruder running in their shop right now gives them faster output than a filament based printer. The extruder also enables a wider range of plastics to be fed into the printer – and it drops the price of the plastics substantially – as native pellet can be used to feed the machine instead of more costly filaments. Larger prints, made faster, can also be machined to tight tolerances where needed. This gives a solution to companies looking to bring the “small” size range of BAM type approach to 3D printing. A lost foam tooling path is in the near term, as is the potential to print a “lost pattern” directly from the printer.
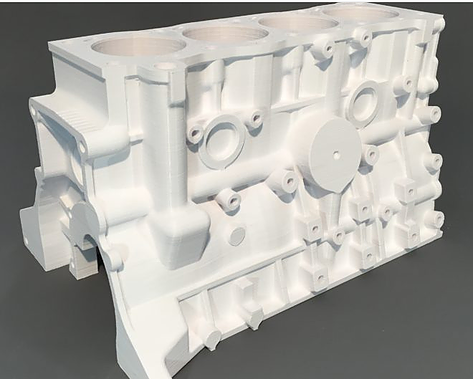
Options for materials are continuing to expand. Standard available materials like ABS and PLA are already in play. Carbon filled plastics, as well as a wide array of other options, are quickly being validated. Check the website to see what’s currently being supported.
So, in short, we at the Metal Fish are very excited about adding this new product to our line card. We hope that our foundry, pattern, and machine shop customers will also be joining the party shortly! (All images courtesy of Titan3D Robotics)